In the daily customs declaration processes, customs inspections are often dreaded as they can disrupt planned work schedules and require on-site attendance with customs brokers. Customs personnel aim to reduce the inspection rate, and understanding certain factors can significantly help.
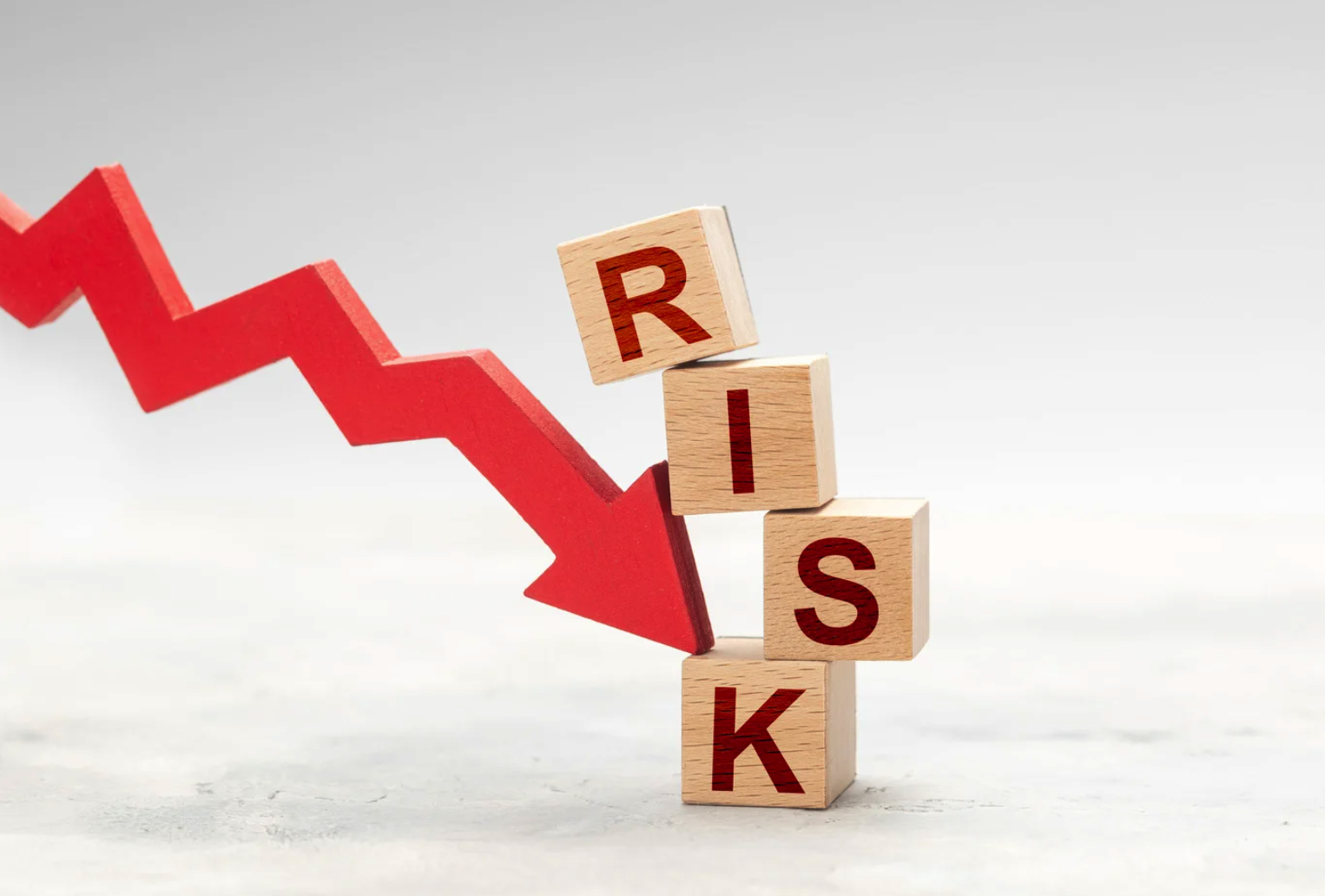
Factors Leading to Customs Inspections
1. Comprehensive Inspection Rate
The comprehensive inspection rate involves random checks by the customs system or through manual control when declaration data enters the system. To improve detection rates, the General Administration of Customs has proposed quantifiable inspection rates: random checks should account for 50% of inspections, with import goods inspection rates above 10% and export goods no less than 5%. System random checks should be at least 3%.
2. Special Events Increasing Inspection Rates
During significant events, customs may increase inspection rates to ensure accuracy in imports. Special actions by customs for specific product categories can lead to nationwide increased inspection rates.
3. Industry-Specific Inspection Rate Increases
If a company in an industry is caught for violations such as high prices or incorrect classifications, customs may increase inspection rates for similar products within that industry during the same period.
4. Trade Method Impact on Inspection Rates
Certain trade methods, like temporary imports and exports or return shipments, undergo batch inspections to verify compliance with "original condition return" requirements. Processing trade, especially new factory imports/exports under the first handbook, is also subject to focused control.
Impact of Customs Inspections on Customs Declarations
1. Inspection Fees
Since 2015, to reduce the burden on import/export companies, the government covers inspection and operation fees if the inspection results match the declaration. However, customs brokers charge a service fee (100-300 RMB) for accompanying inspections, adding to company costs.
2. Overdue Storage Fees
Imported goods require storage in designated warehouses, with a free storage period. Delays due to customs inspections can lead to additional storage fees. For road imports, if inspections are incomplete or result in issues, goods may be detained, incurring daily costs in the thousands of RMB.
3. Export Container Dropping
Exports face potential issues like missed shipping schedules and increased costs due to customs inspections. Poor timing coordination by customs staff can lead to missed departures if inspections occur close to shipping deadlines.
4. Import Production Delays
Many companies fail to account for inspection times in their import schedules, leading to delays. Customs use a risk control database to evaluate declaration risks, flagging high-risk data for control.
Enterprise Factors Leading to Customs Inspections
1. Price Declaration Issues
Customs have a three-level price database (General Administration, direct customs, and subordinate customs). Prices that deviate significantly from these databases trigger manual reviews or controls. Companies should declare prices truthfully.
2. Product Classification Issues
Improperly filled declaration elements by customs staff increase inspection rates. Accurate product classification is crucial.
3. Origin Declaration Issues
Incorrect origin declarations, such as misrepresenting the grade and quantity of imported bananas, can trigger inspections. Accurate origin information is essential.
4. License Document Declaration Issues
Errors in accompanying documents provided by clients can lead to inspections. Ensuring document accuracy is vital.
5. Split Declaration
To avoid licenses, some companies split shipments into smaller batches, which customs can detect through system checks of recent declarations, increasing the risk of inspection.
6. Seasonal Declaration Features
Certain product characteristics and declaration months can increase inspection risks.
7. Enterprise Operation Capability
The company's strength, including registered capital, contract execution, and office attributes, can affect trade background checks and inspection rates.
Methods to Reduce Customs Inspection Rates
1. Effective Document Review Processes
Employing dual-position review processes for document creation and review reduces errors. Adjust and correct erroneous declarations promptly, avoiding risk by ensuring accurate element fillings.
2. Actively Apply for Customs AEO Certification
Companies with sound customs procedures should apply for AEO certification. An AEO advanced certification reduces inspection rates to below 0.9%, while general certification reduces it to below 3%. Maintaining general credit levels results in higher inspection rates.
Applying for AEO advanced certification requires meeting criteria like good financial status and a low error rate in declarations. Seeking professional evaluations can help companies improve systems and achieve higher credit ratings, resulting in lower inspection rates and reduced clearance costs.
By understanding these factors and implementing effective strategies, companies can significantly reduce the likelihood of customs inspections, ensuring smoother and more efficient customs declaration processes.